Recognizing What is Porosity in Welding: Reasons and Solutions
Recognizing What is Porosity in Welding: Reasons and Solutions
Blog Article
The Science Behind Porosity: A Comprehensive Guide for Welders and Fabricators
Understanding the intricate mechanisms behind porosity in welding is essential for welders and fabricators pursuing remarkable craftsmanship. As metalworkers explore the depths of this sensation, they discover a world governed by various factors that affect the development of these small spaces within welds. From the structure of the base materials to the complexities of the welding process itself, a wide variety of variables conspire to either intensify or alleviate the existence of porosity. In this detailed guide, we will untangle the scientific research behind porosity, exploring its results on weld high quality and introduction progressed methods for its control. Join us on this journey with the microcosm of welding imperfections, where accuracy meets understanding in the quest of remarkable welds.
Comprehending Porosity in Welding
FIRST SENTENCE:
Assessment of porosity in welding discloses crucial insights into the stability and high quality of the weld joint. Porosity, identified by the visibility of cavities or voids within the weld metal, is a typical worry in welding procedures. These gaps, otherwise properly attended to, can jeopardize the architectural integrity and mechanical residential properties of the weld, bring about possible failings in the completed product.

To spot and quantify porosity, non-destructive testing approaches such as ultrasonic screening or X-ray evaluation are commonly used. These strategies permit for the recognition of inner issues without endangering the honesty of the weld. By assessing the dimension, form, and circulation of porosity within a weld, welders can make enlightened choices to enhance their welding processes and achieve sounder weld joints.
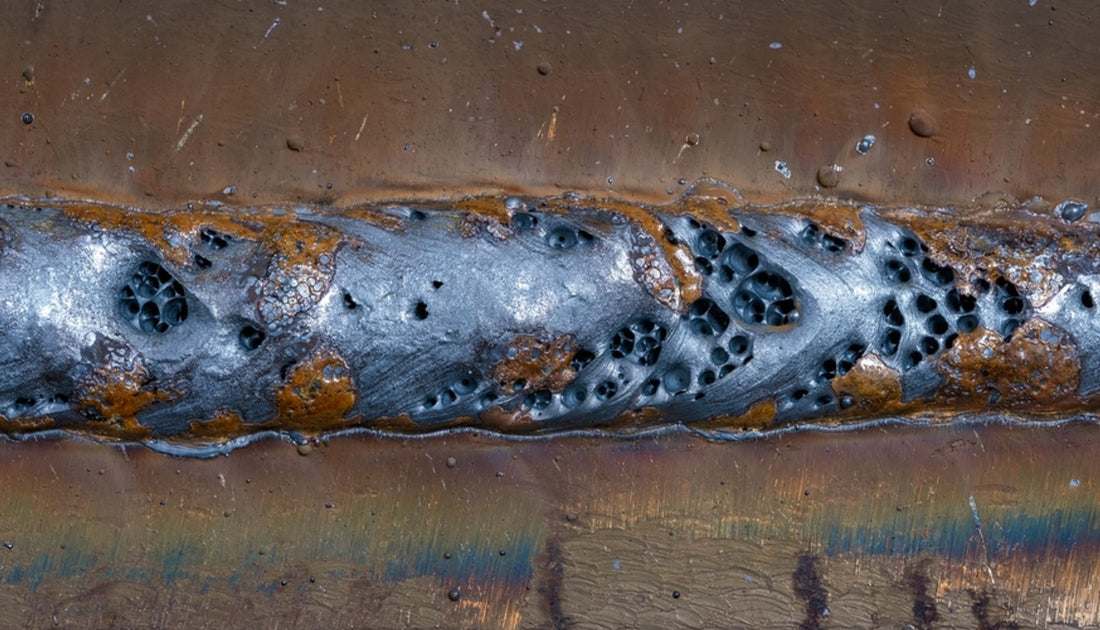
Aspects Influencing Porosity Development
The incident of porosity in welding is influenced by a myriad of variables, ranging from gas securing efficiency to the intricacies of welding specification settings. Welding specifications, consisting of voltage, current, take a trip speed, and electrode type, additionally impact porosity development. The welding strategy utilized, such as gas steel arc welding (GMAW) or shielded metal arc welding (SMAW), can affect porosity development due to variations in warm circulation and gas coverage - What is Porosity.
Impacts of Porosity on Weld Top Quality
Porosity formation dramatically compromises the structural stability and mechanical residential or commercial properties of bonded joints. When porosity exists in a weld, it creates spaces or dental caries within the product, decreasing the general stamina of the joint. These gaps act as anxiety focus factors, making the weld extra susceptible to splitting and failure under load. The existence of porosity likewise deteriorates the weld's resistance to deterioration, as the trapped air or gases within the voids can react with the surrounding atmosphere, causing destruction with time. In addition, porosity can hinder the weld's ability to endure pressure or effect, additional endangering the general top quality and integrity of the bonded framework. In important applications such as aerospace, automotive, or structural constructions, where safety and sturdiness are vital, the damaging impacts of porosity on weld high quality can have serious repercussions, highlighting the value of decreasing porosity via correct welding strategies and treatments.
Techniques to Decrease Porosity
To improve the top quality of welded joints and make sure structural honesty, welders and makers employ details techniques intended at decreasing the development of voids and tooth cavities within the material during the welding procedure. One effective technique to minimize porosity is to make sure correct material preparation. This consists of complete cleansing of the base metal to eliminate any kind of contaminants such as oil, grease, or wetness my site that can contribute to porosity development. Additionally, utilizing the proper welding parameters, such as the appropriate voltage, existing, and take a trip rate, is crucial in stopping porosity. Keeping a get redirected here consistent arc length and angle during welding also helps in reducing the chance of porosity.

Using the ideal welding method, such as back-stepping or employing a weaving activity, can likewise assist distribute warm uniformly and minimize the possibilities of porosity development. By executing these methods, welders can properly minimize porosity and create premium bonded joints.

Advanced Solutions for Porosity Control
Executing sophisticated modern technologies and cutting-edge techniques plays a crucial role in accomplishing premium control over porosity in welding procedures. One sophisticated option is using sophisticated gas combinations. Shielding gases like helium or a blend of argon and hydrogen can help in reducing porosity by offering better arc security and boosted gas insurance coverage. Furthermore, employing advanced welding strategies such as pulsed MIG welding or changed ambience welding can likewise assist reduce porosity problems.
Another innovative remedy entails using advanced welding equipment. As an example, utilizing tools with integrated functions like waveform control and advanced power resources can enhance weld quality and minimize porosity dangers. Additionally, the execution of automated welding systems with exact control over criteria can considerably reduce porosity problems.
Additionally, integrating innovative monitoring and inspection innovations such as real-time X-ray imaging or automated ultrasonic testing can aid in identifying porosity early in the welding procedure, enabling immediate rehabilitative actions. Generally, integrating these sophisticated remedies can greatly boost porosity control and enhance the overall high quality of welded parts.
Verdict
In verdict, comprehending the science behind porosity in welding is vital for welders and producers to create high-quality welds. By recognizing the his comment is here variables affecting porosity formation and implementing techniques to decrease it, welders can improve the overall weld top quality. Advanced remedies for porosity control can even more enhance the welding process and ensure a strong and dependable weld. It is very important for welders to continually enlighten themselves on porosity and implement best techniques to achieve optimum results.
Report this page